Case Studies 4. A car manufacturing plant
Location: A car manufacturing plant.
Description: The plant uses oil free air compressors for its process requirements in the press shop and body welding areas.An Energy Appraisal revealed poor ‘Load’ to ‘Un-load’ ratio of 4 compressors with significant wasted energy.
Solution: The Atlas Copco ZR 250 oil free machines were converted to Variable speed using ABB inverters. Auxiliary drives were fitted to the dryer to match the speed to the compressor.
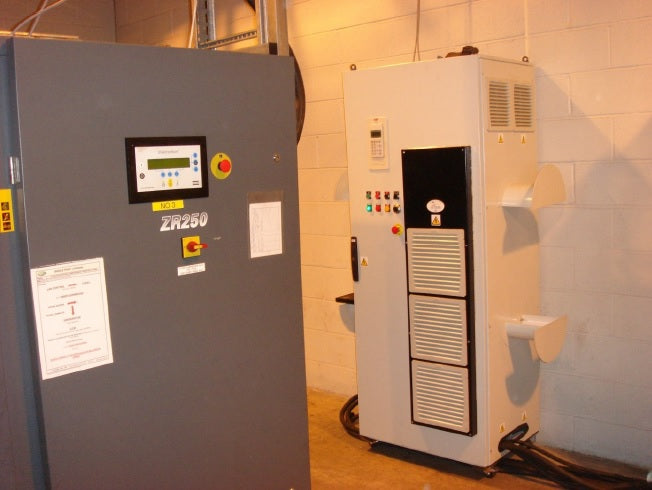
This picture shows the hire drive used to prove savings prior to full installation.
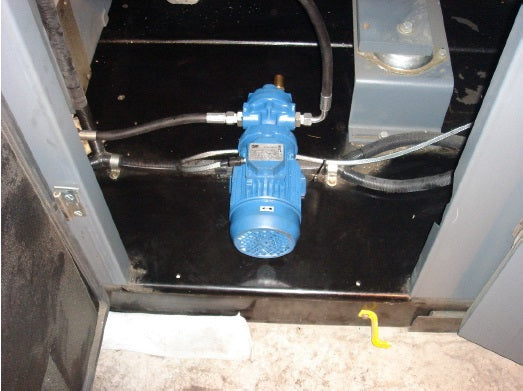
Whilst here we have the fixed speed oil pump added to supply constant oil pressure during slow speed running.The existing EnergAir Compressor Management System software was modified to include the variable speed compressors.
Benefits:
• Total 5 year energy savings of £960,000
• Energy Cost reduction of £1,000 per week per compressor.
• Improved pressure control
• Promotion for the engineer who delivered the project.